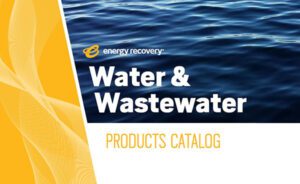
Brochure
In China alone, the water footprint from existing and planned coal-to-chemicals facilities is projected to reach more than 3 billion cubic meters of water per year, and many of these facilities are located in areas that are already struggling to meet demands for water. If all of this toxic wastewater was discharged into local waterways, it would be a public health and ecological disaster, which is why coal-to-chemicals wastewater is required to undergo zero liquid discharge (ZLD) treatment processes so that none of this wastewater is dumped into local waterways. This vital process turns this toxic wastewater into clean water and plays a crucial role in ensuring environmental sustainability, protecting human health, and promoting responsible industrial practices.
Treating wastewater also allows it to be reused within the process, alleviating the demand on the local water supply. Far more energy efficient than traditional thermal processes, reverse osmosis (RO) membrane technology—in conjunction with energy recovery devices (ERDs)—can vastly reduce the energy consumption and costs required to reach ZLD. Plus, these types of systems are more compact and more flexible to design and install than traditional thermal systems, and offer the ability to offset some treatment costs.
Including our gold-standard PX Q series, our high-pressure PX products provide unmatched energy recovery for large and small seawater reverse osmosis (SWRO) desalination and water treatment systems.
Our most efficient, highest-capacity PX for seawater reverse osmosis desalination facilities.
Press Release
SAN LEANDRO, Calif. – May 21, 2025 — Energy Recovery (NASDAQ: ERII) today reported contract awards totaling over $7 million for its PX® Pressure Exchanger® (PX) energy...
Press Release
SAN LEANDRO, Calif. – Feb. 27, 2025 — Energy Recovery, Inc. (Nasdaq: ERII) today announced the results of recently conducted testing which concludes that the PX® Pressure®...
Press Release
SAN LEANDRO, Calif. – Feb. 26, 2025 — Energy Recovery, Inc. (Nasdaq: ERII) today announced its Board of Directors approved a share repurchase program to purchase up to $30...
Press Release
SAN LEANDRO, Calif. – Feb. 26, 2025 — Energy Recovery, Inc. (Nasdaq: ERII) today announced the appointment of a new Chief Technology Officer and Vice President, Wastewater....