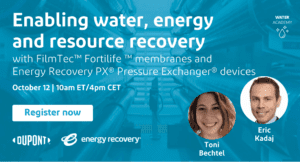
On-demand Webinars and Podcasts
Brine (often seen as a waste product) can contain valuable and sometimes rare metals, salts, and minerals that are highly sought after in other industries, including lithium-ion battery manufacturing, agriculture, textiles, construction, and many more. In some cases, the mineral byproducts of treating water can be more valuable than the produced freshwater itself. The types of resources that can be recovered from wastewater treatment are extensive, and their uses are nearly endless. Even manure from animal farming can be turned into biogas and fertilizer, while recovering water suitable for environmental discharge.
While resource recovery (also known as brine mining, nutrient recovery, resource extraction, and waste valorization) has been utilized in some form for decades, in recent years there has been a surge of interest and investment in maximizing the potential of this untapped resource. Reverse osmosis (RO) membrane technology has been used to recover all of the resources listed here, and utilizing energy recovery devices (ERDs) within RO systems significantly reduces the energy consumption and costs required to treat wastewater and extract these valuable minerals. Some of our customers have already utilized separation technology to successfully extract and commercialize minerals from their waste stream, while also further reducing project emissions for rebates and potential carbon credits.
Including our gold-standard PX Q series, our high-pressure PX products provide unmatched energy recovery for large and small seawater reverse osmosis (SWRO) desalination and water treatment systems.
Ideal for brackish water reverse osmosis and water reuse in municipal and industrial applications, our low-pressure PX solutions offer substantial energy savings and ease of integration.
On-demand Webinars and Podcasts
On-demand Webinars and Podcasts
Brochure
Press Release
SAN LEANDRO, Calif. – May 21, 2025 — Energy Recovery (NASDAQ: ERII) today reported contract awards totaling over $7 million for its PX® Pressure Exchanger® (PX) energy...
Press Release
SAN LEANDRO, Calif. – Feb. 27, 2025 — Energy Recovery, Inc. (Nasdaq: ERII) today announced the results of recently conducted testing which concludes that the PX® Pressure®...
Press Release
SAN LEANDRO, Calif. – Feb. 26, 2025 — Energy Recovery, Inc. (Nasdaq: ERII) today announced its Board of Directors approved a share repurchase program to purchase up to $30...
Press Release
SAN LEANDRO, Calif. – Feb. 26, 2025 — Energy Recovery, Inc. (Nasdaq: ERII) today announced the appointment of a new Chief Technology Officer and Vice President, Wastewater....