Reducing energy costs
Treating industrial wastewater from textile production is essential for environmental protection, water conservation, and regulatory compliance, which is why countries such as China and India (two of the world’s biggest textiles producers) are tightening regulations on manufacturers. Wastewater treatment also allows for water recovery and reuse, reducing the strain on freshwater resources. However, it can be an energy intensive process and create an additional cost burden on manufacturers. Textile effluents can be especially toxic and difficult to clean.
Membrane technology, in conjunction with energy recovery devices (ERDs), can vastly reduce the energy consumption (resulting in significant OPEX savings) and costs required to treat wastewater in comparison with traditional methods. They’re also more compact and more flexible to design and install than thermal systems, and offer a higher rate of water recovery, allowing for more of the resulting freshwater to be re-used and reduce water intake. Finally, a membrane system allows for salts, dyes, and other components to be recovered from the wastewater and reused to reduce and offset costs.
Featured Products
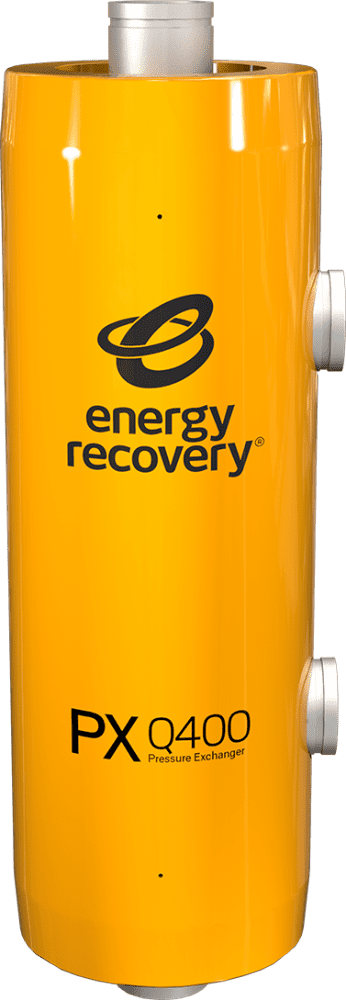
High-Pressure PX
Including our gold-standard PX Q series, our high-pressure PX products provide unmatched energy recovery for large and small seawater reverse osmosis (SWRO) desalination and water treatment systems.
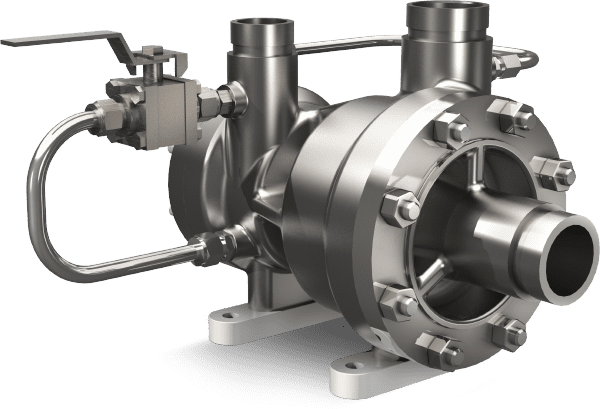
AT Turbocharger
The AT turbocharger is an efficient, versatile, and reliable solution designed with a compact footprint—no instrumentation or additional equipment is necessary. In addition, it requires minimal installation time and operator training. With the turbocharger’s completely removable and replaceable hydraulics, plant staff can quickly and inexpensively change operating conditions as needed while...
Resources
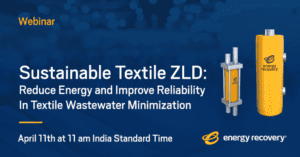
On-demand Webinars and Podcasts
Sustainable Textile ZLD – Reduce Energy and Improve...
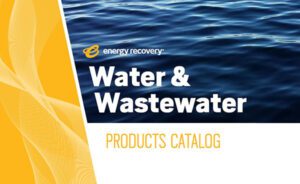
Brochure
Water & Wastewater Products Catalog
Recent News
Press Release
Energy Recovery Announces Desalination Contracts Totaling...
SAN LEANDRO, Calif. – May 21, 2025 — Energy Recovery (NASDAQ: ERII) today reported contract awards totaling over $7 million for its PX® Pressure Exchanger® (PX) energy...
Press Release
Energy Recovery Announces Expanded 30-Year Pressure...
SAN LEANDRO, Calif. – Feb. 27, 2025 — Energy Recovery, Inc. (Nasdaq: ERII) today announced the results of recently conducted testing which concludes that the PX® Pressure®...
Press Release
Energy Recovery Announces New Share Repurchase...
SAN LEANDRO, Calif. – Feb. 26, 2025 — Energy Recovery, Inc. (Nasdaq: ERII) today announced its Board of Directors approved a share repurchase program to purchase up to $30...
Press Release
Energy Recovery Appoints New CTO and...
SAN LEANDRO, Calif. – Feb. 26, 2025 — Energy Recovery, Inc. (Nasdaq: ERII) today announced the appointment of a new Chief Technology Officer and Vice President, Wastewater....