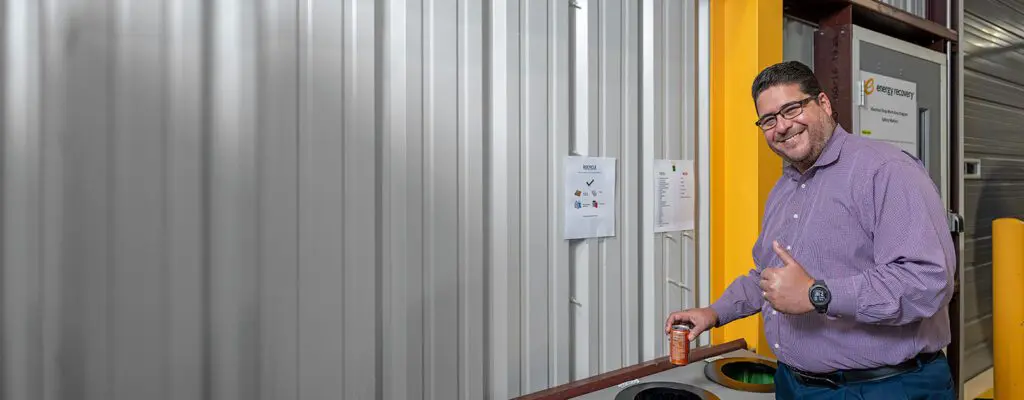
Engineering Innovative and Forward-Thinking Solutions
Environmental Management
Energy Recovery helps customers save energy and adapt to an evolving climate. We have formalized our commitment to reduce emissions through our products, as well as in our own operations. Our business objective to support customer success aligns with better environmental outcomes, as energy efficiency and reduced waste saves on operational expenses and resources.
Current Goals
Goal 1
Goal 2
Goal 3
Goal 4
Goal 5
Reduce scope 1 and 2 emissions intensity 65% by 2026 from 2021 baseline
As part of our business growth strategy, we set an ambitious, but achievable, emissions reduction goal focused on intensity rather than absolute emissions. We’re making strong progress toward this goal by using 100% renewable electricity across all our facilities, a transition that began in 2022 and has already reduced our market-based Scope 2 emissions by 92%. We’re also working to cut energy use in our manufacturing processes, particularly in reducing electricity and natural gas consumption. Our Scope 1 emissions primarily come from the natural gas-powered kilns used to fire the ceramic cartridges at the heart of our pressure exchangers. To address this, we’re working to optimize kiln cycles and reduce natural gas consumption while maintaining product quality and process integrity.
Altogether, we’ve reduced our Scope 1 and 2 emissions intensity by more than 52% from our 2021 baseline. For a deeper dive, please see our data performance tables and GHG emissions details in the 2024 Sustainability Performance Summary.
Reduce emissions intensity to 10 MT CO2e per million dollars of revenue by 2026 from 2021 baseline
Target:
10
2021 Baseline:
29
2024 Value:
14
Status:
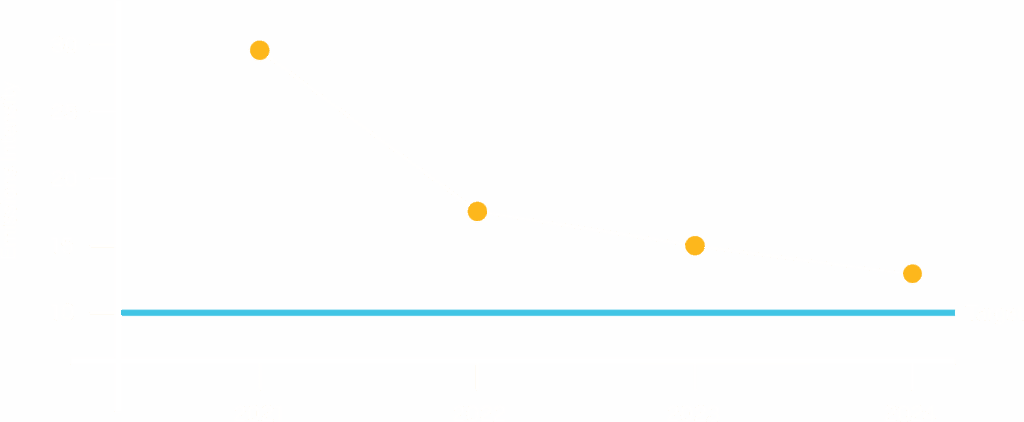
Double emissions reductions from our products by 2025
At Energy Recovery, developing technologies that save energy and help our customers adapt to a changing climate is core to both our business and sustainability strategy. Back in 2020, we set an ambitious goal to double our impact by 2025—through new applications, innovations, and expansion into new markets and industries. We’re proud to share that we met this goal ahead of schedule. In 2024 alone, our technologies helped avoid over 22 million metric tons of CO₂ emissions, saving our customers 47.4 TWh of energy and $7.2 billion in costs. While we will continue to report on this key performance indicator, we won’t be setting a new target, as these metrics are closely tied to our broader revenue growth goals.
Target:
20.8 million
2019 Baseline:
10.4 million
2024 Value:
22.5 million
Status:
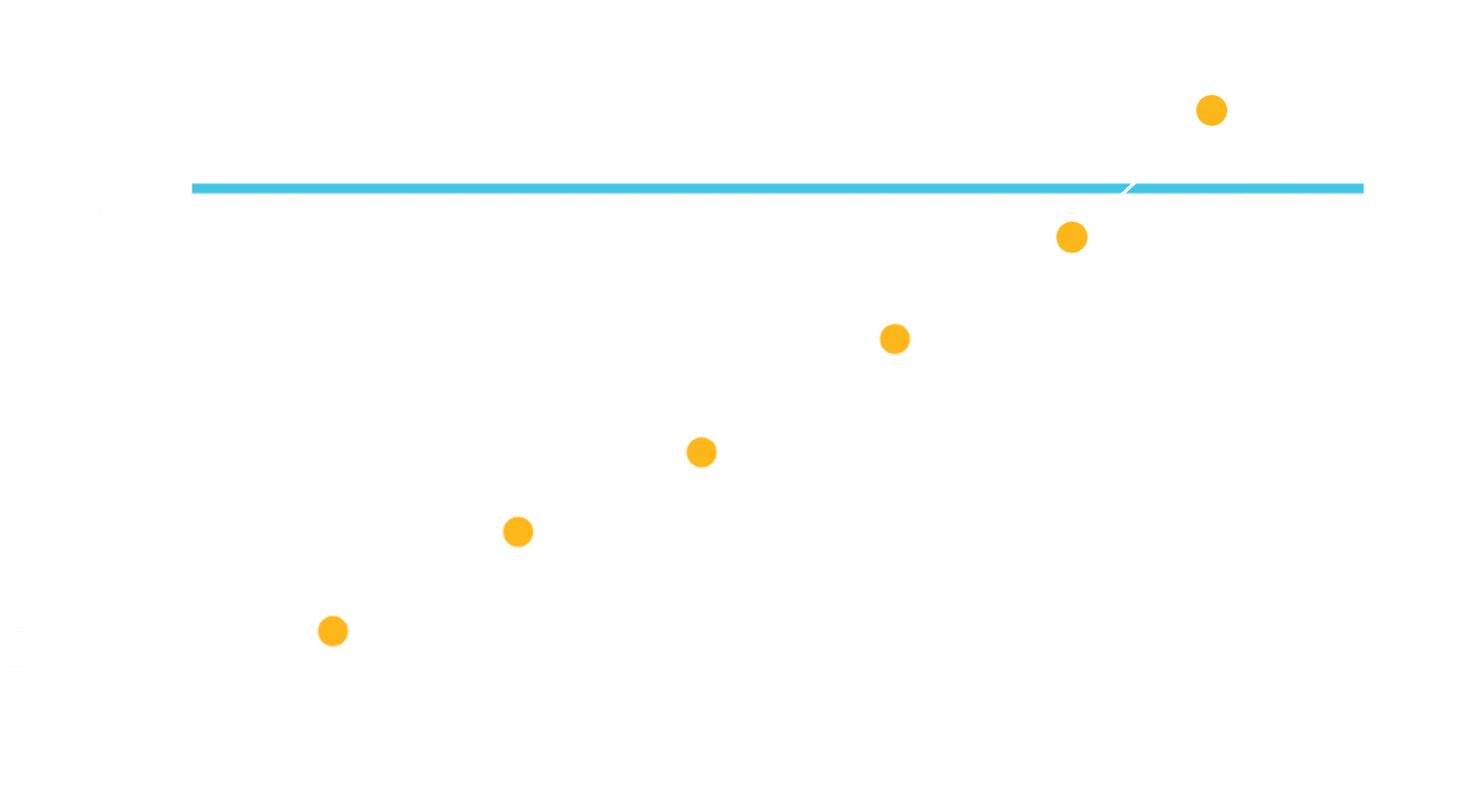
Further integrate sustainability into our product development process to understand a product’s lifecycle impact
Innovation is a key part of Energy Recovery’s winning culture and decades of success. It drives our growth, helps us maintain market leadership in desalination, and supports our commitment to excellence as we expand into new markets. As part of our New Product Development process, we’ve always considered the broader implications of a product’s impact on sustainability. In keeping with that philosophy, we’re working to formalize and streamline this evaluation through a sustainability scorecard that assesses both the benefits our products bring to customers and the environmental impacts associated with producing, using, and disposing of them. We’ve made solid progress: after conducting best practice research, including a review of third-party frameworks and peer company approaches, we’re on track to develop the first draft of the scorecard by the end of the year with 2026 targeted for piloting and adoption of the tool.
Target:
Develop scorecard by end of 2026
Status:
Reduce waste generated in our operations
In conjunction with our ISO 14001 Environmental Management System certification and our commitment to continuous improvement, we remain focused on reducing resource consumption at our facilities through waste management strategies that emphasize reuse, recovery, and recycling. Building on past efforts, this goal formalizes our commitment with measurable targets to keep us accountable.
We’re proud to share that we’ve achieved a major milestone: over 90% of our alumina powder waste is now recycled, and none of it goes to landfill. One hundred percent of this waste is either internally reused or sent to a trusted external partner for recycling. Internally, we recover excess alumina powder from the manufacturing process, screen it for reuse, and reintegrate it into production. This closed-loop process not only cuts down on waste but also reduces our need for raw materials. We’ve also made progress on broader waste goals, including recycling 100% of our scrap metal, launching recycling and compost streams at all our facilities, and rolling out a pallet collection and recycling program.
We are introducing two new waste targets that represent the next phase of our journey toward minimizing the environmental impact of our manufacturing operations.
Firstly, as part of our continuous improvement efforts, our operations team identified the reduction of non-conforming ceramic parts, or scrap, as a priority. In 2025, we aim to reduce our scrap rate to 2.5%, compared to 3.7% in 2024. This metric reflects the percentage of scrapped ceramic components, such as those that break during processing or fail quality inspections, relative to finished ceramic components. Ceramics typically have higher scrap rates than non-ceramic materials, due to their complex processing requirements. Given that ceramic components are a critical component in our PX® devices, optimizing yield is both a sustainability and operational priority. These efforts not only reduce the volume of non-hazardous waste sent to landfill but also drive cost savings.
Secondly, to enhance transparency and support continuous improvement in our waste management practices, we will begin reporting hazardous waste data annually starting in 2025. The total amount of hazardous waste generated in 2024 is included in our Environmental Performance Data, and we plan to expand the detail and scope of this reporting by 2027.
Commit to setting a hazardous and non-hazardous waste goal by 2025
Target:
Set goal by end of 2025
Status:
Recycle over 90% of alumina powder waste
Target:
Above 90%
2024 Value:
100%
Status:
Maintain scrap waste sent to landfill rate below 2.5%
Status:
Disclose hazardous waste data annually starting in 2025, with expanded reporting by 2027, to enable continuous improvement
Status:
Reduce water used in operations
As a company founded on advancing energy-efficient technologies in the desalination industry, we recognize the growing urgency of global water challenges; challenges that are intensified by climate change and worsening water scarcity. This is especially relevant to our operations, as both of our manufacturing facilities in Northern California are located in areas classified as high to extremely high water risk zones (according to the World Resources Institute’s Aqueduct Water Risk Atlas). These physical risks, including water stress, depletion, and flooding, underscore the importance of proactive water management.
To strengthen our long-term operational resilience, we’ve established Energy Recovery’s first-ever water conservation target: to maintain water withdrawal intensity below 0.06 megaliters per million dollars of revenue. This measurable goal allows us to track progress as we scale and ensures that water efficiency remains a priority across our facilities.
With water meters now installed at all production sites, we can monitor usage by process and make more targeted improvements. For example, several of our production test loops in drought-prone California have been retrofitted to reclaim and recycle water, saving an estimated 75,000 liters per year. These efforts reflect our broader commitment to responsible water stewardship and to leading by example in the water treatment sector.
Commit to setting a water reduction goal by 2025
Target:
Set goal by end of 2025
Status:
Maintain water withdrawal intensity below 0.06 megaliters per million dollars of revenue
2024 Value:
<0.05
Status:
Highlights
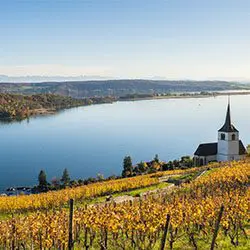
Customer Spotlight
Revolutionizing Water Reuse in Switzerland
A potable water treatment plant in Biel, Switzerland, serving 70,000 residents in Biel and the surrounding region, was redesigned to improve water purity and regional water security while drastically cutting energy use. Like many regions around the world, Switzerland is facing the challenge of water scarcity and is incorporating water reuse into its long-term strategy to secure a sustainable supply of clean water. Energie Service Biel/Bienne (ESB), in partnership with Membratec S.A., implemented a reverse osmosis (RO) system enhanced by Energy Recovery’s Low-Pressure PX® Pressure Exchanger®, which helps to maximize the energy efficiency and long-term affordability of the system.
The Low-Pressure PX brought the system’s specific energy consumption below 0.6 kWh/m³, delivering estimated savings of $120,000 per year and 269 MT CO2e emissions avoided annually, supporting Switzerland’s net zero emissions goal. This treatment facility is an important component of the region’s efforts to secure reliable, clean water for future generations, and Energy Recovery is proud to support this progress. Read more here.
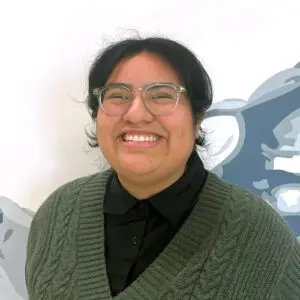
Employee Spotlight
Zitlali Lustre
Industrial Engineering Intern (now full-time Manufacturing Engineer)
For Zitlali Lustre’s internship project, she took on the task of digitizing Energy Recovery’s hard-grind manufacturing inspection process. Before this project was completed, staff would fill out a physical paper form documenting each step of the hard-grind process from fitting to inspection. At a later stage in the process, these forms would need to be scanned into a shared drive and filed away. So, while manufacturing data was backed up and stored digitally, it was not easily accessible and had to be compiled manually.
Zitlali worked with manufacturing and IT to develop a new digital process that was just as quick to complete for manufacturing staff but would make the manufacturing data easier to find. After starting with one successful pilot, the digital spec sheets were scaled to cover every part and implemented in both the San Leandro, CA and Tracy, CA production sites. Now our team uses SharePoint to record and input the rotor and sleeve manufacturing and inspection data, which is easily cross-referenced by serial numbers and goes into a centralized dashboard to quickly and effectively track data and allow us to identify and respond to any potential issues quickly. The process also improved the sustainability of our operations by reducing waste generated in manufacturing.
The most gratifying part has been to work with the manufacturing staff to learn about their process and how to make the digital forms work for them. I still meet with them regularly to check in on how the digital forms are working, and it’s satisfying to see it come to life.
Zitlali Lustre
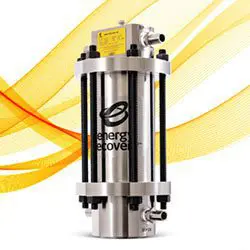
Customer Spotlight
Cutting Water Use in Supermarket Refrigeration
A Northern California supermarket aimed to enhance the sustainability of its CO₂ refrigeration system by reducing water and energy consumption. In summer 2024, they retrofitted their system with Energy Recovery’s PX G1300 pressure exchanger through a compact, add-on module. This upgrade led to a 98% reduction in water usage and energy savings of up to 14%, aligning with the store’s environmental objectives. Read more here.
Last Updated: June 2025
For details on data methodology and definitions, please see our most recent annual performance report.
Questions? Let’s Talk.
We believe in nurturing long-lasting partnerships with our customers to achieve environmentally sustainable and profitable operations—and it all starts here.